“Smart loading, smart processing, smart networking – these three key topics are going to shape the industrial production world in the upcoming five years,” underlines Henrik A. Schunk ahead of EMO 2019. “The core objective is intelligent simplification of industrial production.” Up to now, process stability and efficiency of the individual operations dominated, modern applications will offer a higher degree of flexibility in the process chain, and will provide detailed process data, according to the experts at SCHUNK.
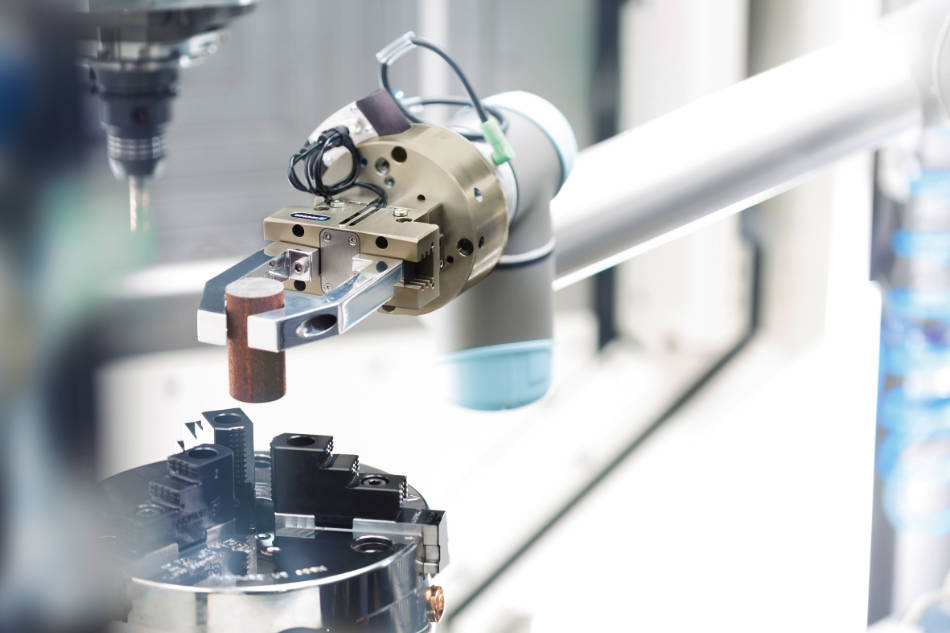
The smart iTENDO from SCHUNK enables real-time process monitoring and control directly on the tool. The geometry and performance data of the toolholders remain unchanged no matter if it is equipped with a sensor system or not.
“Our clamping devices and gripping systems will enable detailed monitoring of the production process in real time and autonomously carry out corresponding reactions,” says the Chief Executive Officer. The best example of this: The sensory precision toolholder iTENDO, which will be available for pilot applications from fall. It allows complete status monitoring and documentation of process stability, unmanned limit value monitoring, tool breakage detection, as well as real-time control of the speed of rotation and feed rate. If the cut becomes unstable, the integrated intelligence intervenes immediately in real time, and with no action required from the operator: depending on the situation, the process is stopped, reduced to previously defined basic parameters, or adapted until the cut returns to a stable range. Digital twins of the toolholder series TENDO, TRIBOS and SINO based on DIN 4000 will also ensure consistency of data throughout the entire CAD/CAM process chain. They provide the perfect preconditions for simulations, collision observations, and for shopfloor management.
The specially designed modular system SCHUNK end-of-arm for lightweight robots from Universal Robots enables particularly simple and cost-effective machine loading.
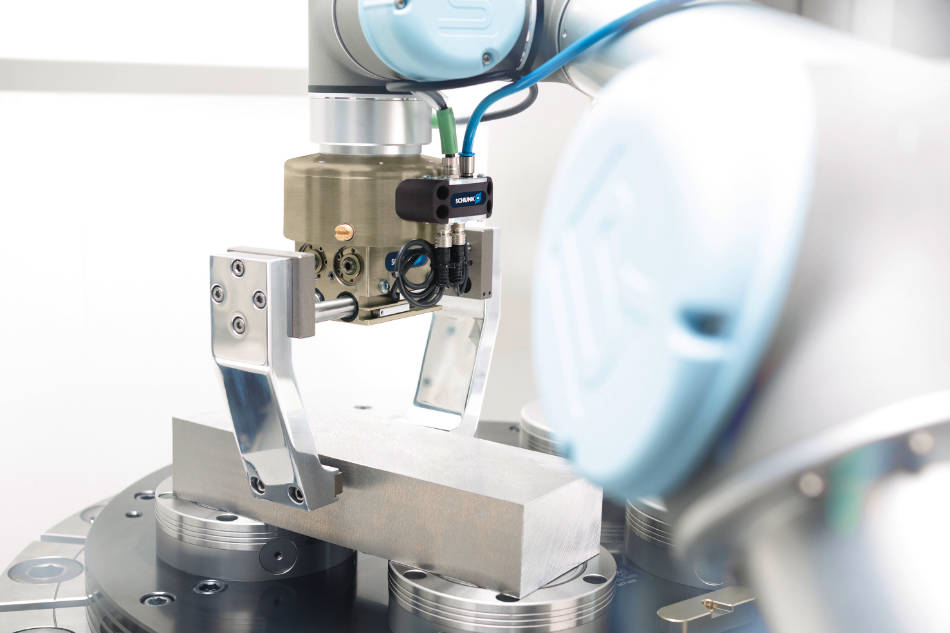
Focus on automated machine loading
In the field of VERO-S quick-change pallet technology, SCHUNK is introducing a sensory quick-change pallet module for the first time, which enables permanent monitoring of the pull-down force and the clamping slide position, as well as of workpiece or pallet presence. In addition, new VERO-S special components will be presented for the aviation industry, 3D printing, and direct workpiece clamping. Besides the following highlights, SCHUNK will showcase sophisticated concepts with an emphasis on automated machine loading. Lean automated solutions, simple to implement up to cost-attractive ones, applications with lightweight robots to convenient palletizing solutions for flexible small-batch production up to ergonomic, collaborative solutions with the long-stroke gripper Co-act EGL-C in direct interaction with humans for form-fit handling of workpieces weighing up to 8 kg. SCHUNK at EMO 2019: Hall 3, Booth D30
The specially designed modular system SCHUNK end-of-arm for lightweight robots from Universal Robots enables particularly simple and cost-effective machine loading.
More infomrations: SCHUNK Intec GmbH, Friedrich-Schunk-Straße 1, 4511 Allhaming, Austria, info@at.schunk.com, www.schunk.com